Engineering
Gear calculation and gear train design
Santa Fe ECS, provides calculation, analysis and design services for gears and mechanical transmissions.
With our customized calculation services, we help you to successfully execute your gear and mechanical drive engineering projects and to accelerate and facilitate your product development. Our offer ranges from the performance of extensive strength calculations and optimization analyses to the creation of verifiable reports.
All calculations are supported by modern software and calculation methods and are based on national and international standards and guidelines e.g. AGMA, API, VDI, DIN EN, ISO, FKM, Eurocode, AD, DNV.
Types of gears we calculate and design:
Spur gears: Spur gears are one of the most common types of gears we calculate and design. These gears have straight teeth parallel to the gear shaft. They are widely used in various applications such as machinery, automotive transmissions and industrial equipment.
Helical gears: Helical gears are another type of gear we specialize in. These gears have angled teeth, which allow for smoother and quieter operation compared to spur gears. Helical gears are commonly used in applications that require high power transmission, such as automotive transmissions and heavy machinery.
Planetary gears: Planetary gears, also known as epicyclic gears, are another type of gearing that we have mastered. These gears consist of a central gear called a sun gear, surrounded by several gears called satellite gears, and an outer ring gear called a ring gear. Planetary gears offer high transmission ratios and torque capacity, making them suitable for applications requiring compact, high-efficiency power transmission, such as automotive transmissions, aerospace systems and industrial machinery.
Engineering key points
- Extensive experience in gear engineering
- In-depth knowledge of gear manufacturing materials
- Expertise in gear heat treatment
- Extensive experience in the use of gear calculation software
- Use of simulation programs using finite element techniques (FEM)
- Use of CAD systems for gear design
- Long experience in projects of planetary gear design for motion control
Gear Design Flowchart
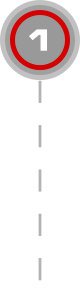
Step 1
Your idea
The first step starts with you. Present us your idea, we listen to you
• The customer provides Santa Fe ECS with all documentation related to the project, such as product descriptions, key features, constraints, sketches, visual inspirations, etc.
• Review of the customer’s objectives.
• The idea
• The market. the competition. product life on market.
• Annual production
• Time required for project execution, etc.
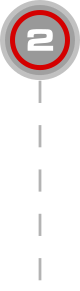
Step 2
Feasibility study
Technical feasibility study of the customer’s project
• Generation of product specifications
• Project’s phases
• Risk analysis.
• Economic and Technical constraints
• Review of required certifications as IP grade, ATEX, CE, UL, etc
• Roadmap for achieving the customer’s objectives
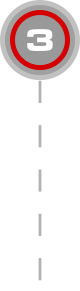
Step 3
Quotation and PO
Once Santa Fe ECS has sufficient information to fully understand the project and its objectives, a quotation will be generated and sent to the customer for approval.
• Presentation of the quotation. price for each phase of the project.
• PO and acceptance of the quotation
• The customer assigns a contact person for consultations and project follow up
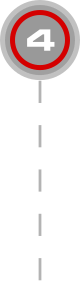
Step 4
Project development
• The mechanical transmission to be designed
• Duty cycle, environmental conditions, required service life
• Cost approach
• Gear analysis
• Possible gear combinations, comparison and selection of the optimum solution.
• Optimum steels and heat treatment
• Calculation according to the standards (AGMA, ISO, etc)
• Tooth quality and safety analysis
• Profile and tooth trace modifications
• Operating temperature and optimal lubrication
• Noise and vibration analysis
• Wear and failure analysis
• Performance
• Transmission shafts
• Steel selection and sizing
• Torsional analysis
• Selecting the right bearings and service life
• Shaft load distribution optimization.
• Noise and vibration analysis
• Failure analysis. Finite element analysis (FEA)
• Transmission housing
• Steel selection
• Stress analysis by FEM method
• Gear and shaft misalignments
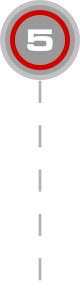
Step 5
Mechanical transmission design
• 3D modeling
• 2D drawings
• Bill of materials
• Manufacturing techniques
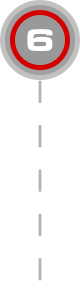
Step 6
Project review and approval
Once the calculations and analysis are completed, a 3D or digital rendering is sent to the customer for review.
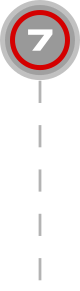
Step 7
Final report
• Preparation of the final report and project summary
• Generate manufacturing documentation
• 2D drawings for the manufacture of parts
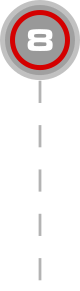
Step 8
Manufacturer And Supplier Selection
• Find and compare quotes from Manufacturers
• Determine quality and reliability of manufacturers and suppliers
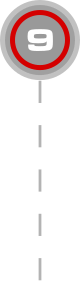
Step 9
Review of pre-production gear samples
Customer is supported in the quality review of the first sample units.
• Sample quality review
• Sample measurement review
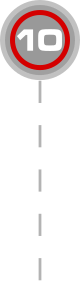
Step 10
Review of pre-production housing samples
Customer is supported in the quality review of the first housing units.
• Sample quality review
• Sample measurement review
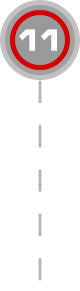
Step 11
Review of Tests
Customer is supported in mechanical transmission testing.
• Comparison of theoretical parameters with tested parameters.
• Tooth flank contact pattern verification
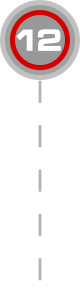
Step 12
Certification
Customer is supported in mechanical transmission testing.
• Comparison of theoretical parameters with tested parameters.
• Tooth flank contact pattern verification
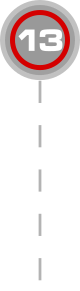
Step 13
Customer and Santa Fe ECS approve mass production of the product
• Once all tests have been completed, customer and Santa Fe ECS approve mass production of the product
• The document for the mass production of products is drawn up.